こんにちは、スクーティー代表のかけやと申します。
弊社は生成AIを強みとするベトナムオフショア開発・ラボ型開発や、生成AIコンサルティングなどのサービスを提供しており、最近はありがたいことに生成AIと連携したシステム開発のご依頼を数多く頂いています。
半導体製造において仕様書データベース化の自動化は、初期のプロセス開発や大量データの効率的な管理に不可欠な要素です。膨大なパラメトリックデータの取得、処理、各種レポート作成、グラフ化は、従来の手作業では多大な労力と時間を要していました。
本記事では、仕様書データベース自動化システムの構造と各機能、RoviSysによるリアルタイム化、Opcenterによる半導体製造プロセスの最適化、IBM SiView Standardによる高度な製造管理、さらにRITdbおよびWAT/PCMデータの取り組みについて詳細に解説します。各見出し毎に全角500文字以上の解説を行い、具体的な事例や定量的な成果、図表や箇条書きにより分かりやすく構成されています。
半導体仕様書データベース化の自動化システムとは
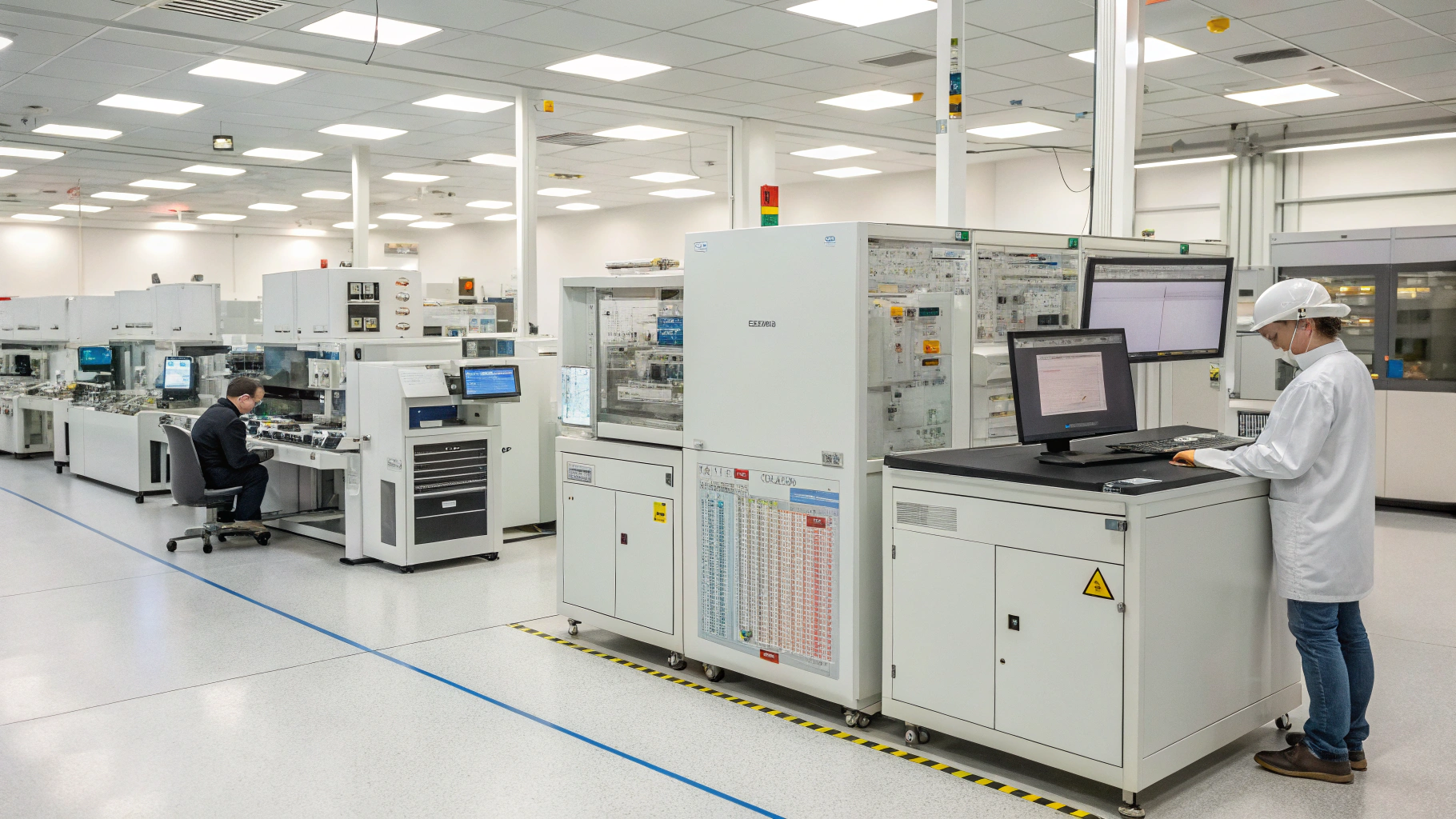
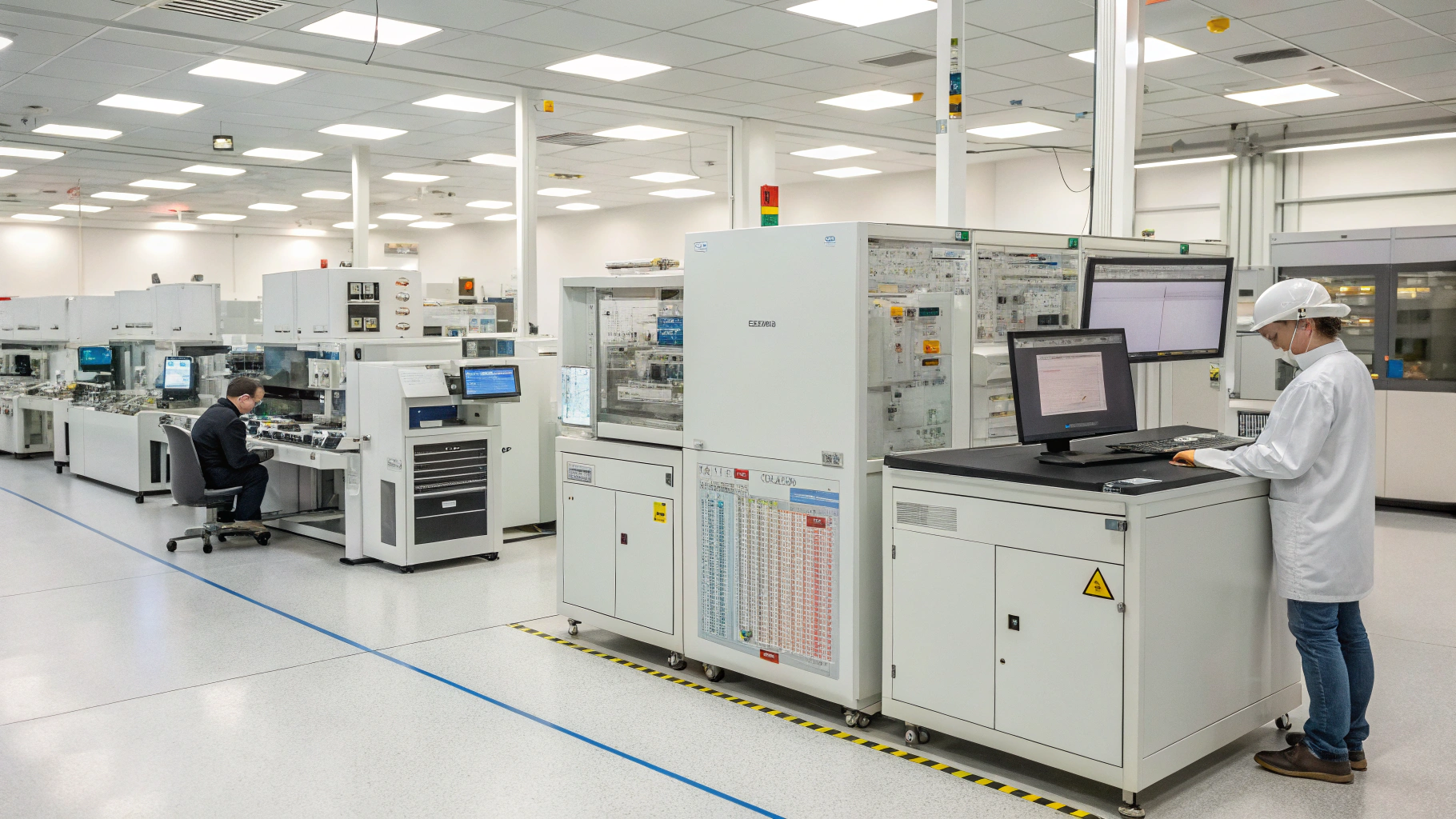
まず、OCR について知りたいという方は、ぜひこちらの記事を先にご覧ください。
関連記事:Tesseract OCRの完全解説:インストールから活用事例、最新技術との比較まで
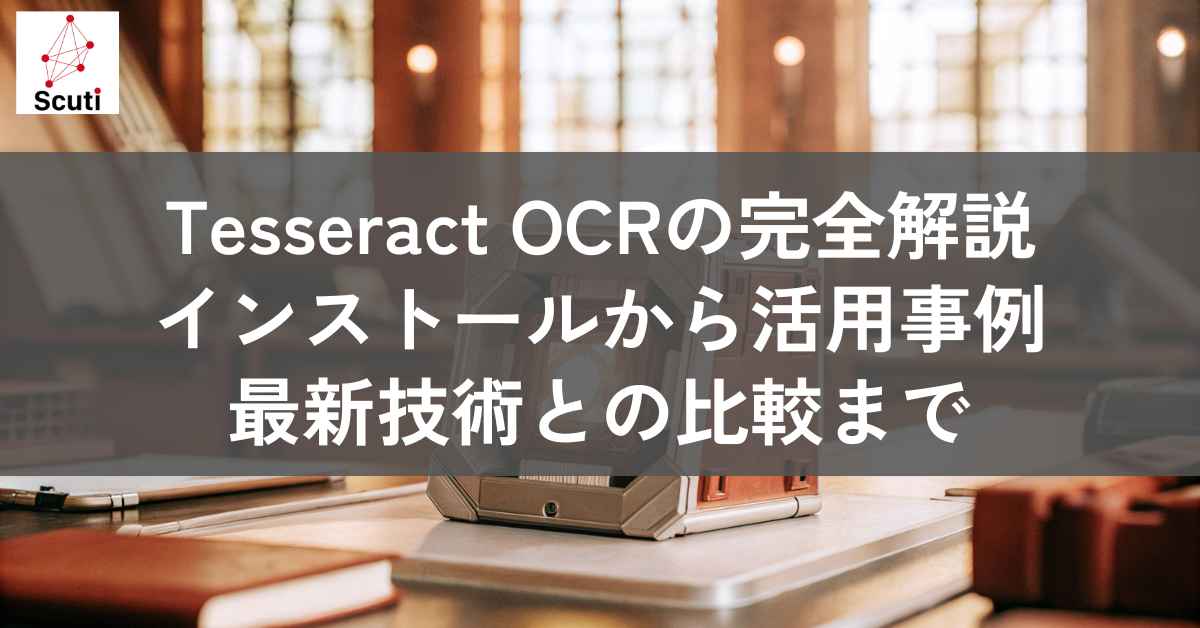
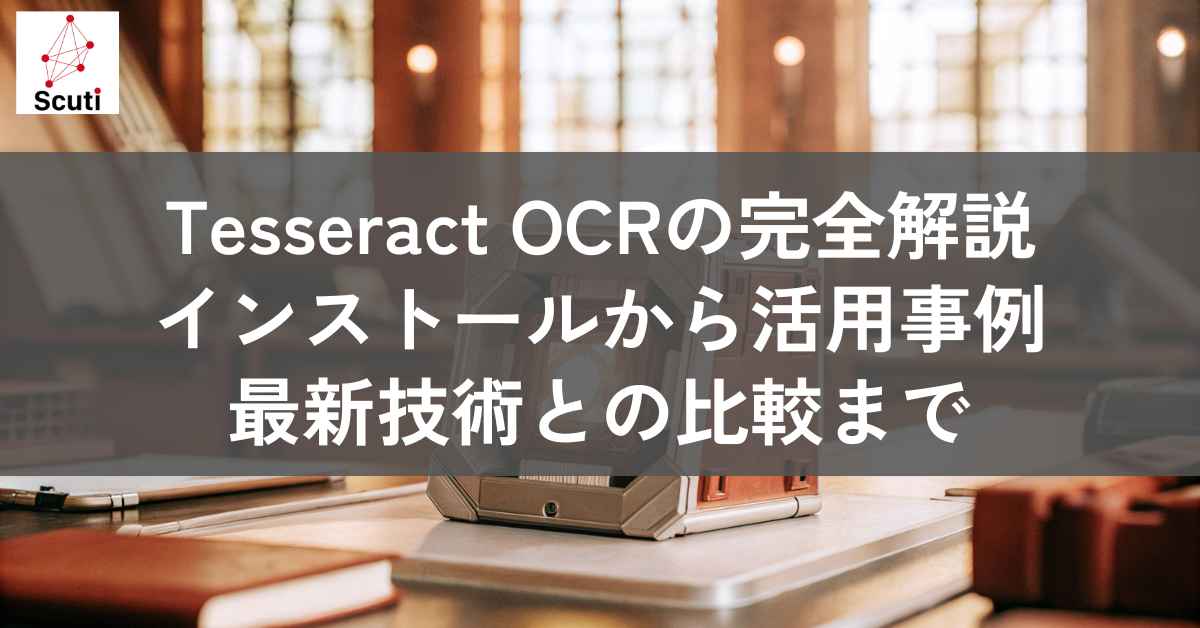
関連記事:olmOCR : PDFテキスト抽出を1/32のコストで実現!?
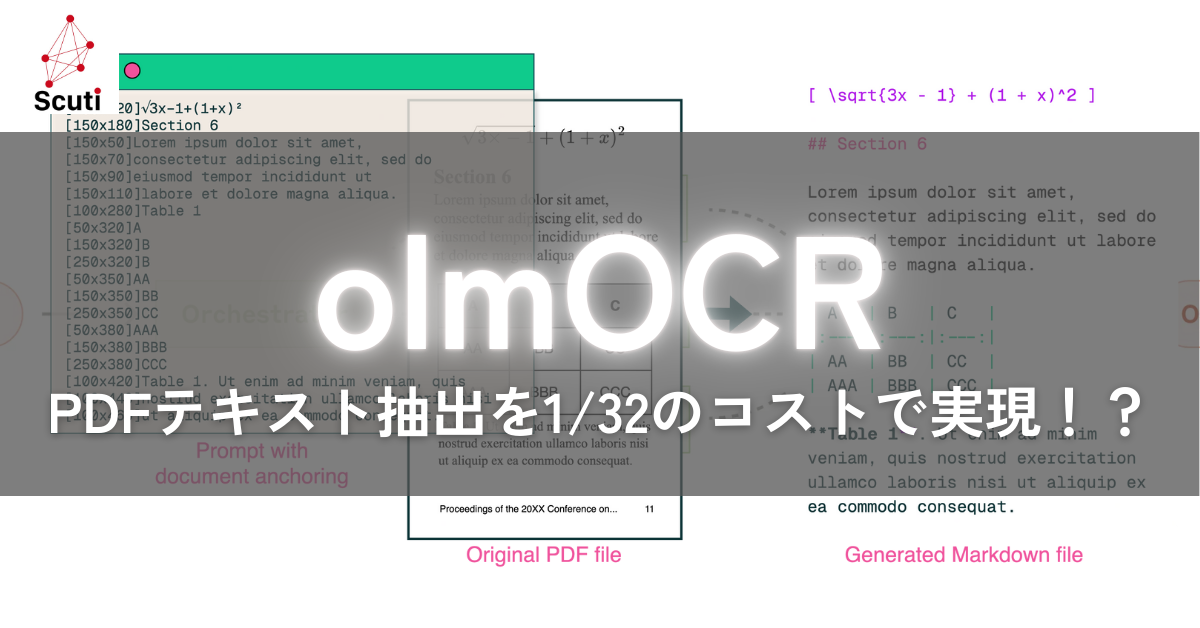
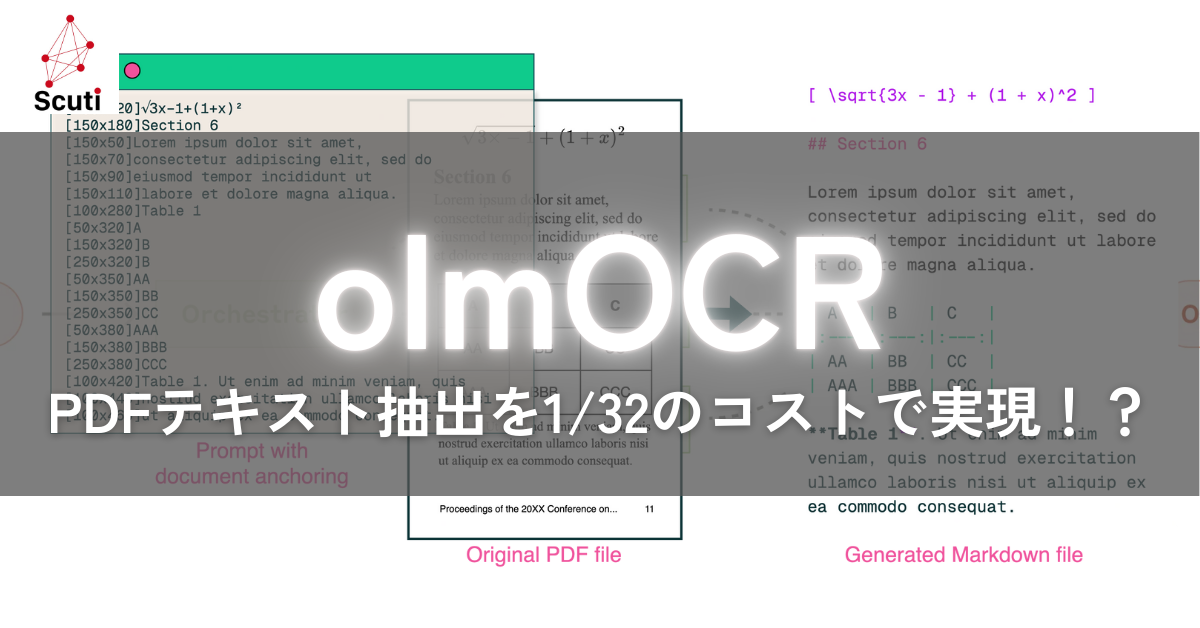
関連動画:【2025最近】知らなきゃ損!電子部品カタログ作業を生成AI-OCRで90%効率化する方法
自動化システムの設計と機能
半導体製造プロセスにおいて、仕様書データベース化の自動化システムは、エンジニアが生成済みのレポートを簡易に閲覧し、必要なデータを迅速に視覚化・取得できるように設計されています。具体的には、仕様ファイルと呼ばれる入力データが軸となり、ここには各パラメータの名称、詳細な説明、上限および下限のスペック、目標値、そして要約レポート作成用のカテゴリ情報が体系的に定義されています。仕様ファイルの構造は、複数のパラメータが階層的に整理され、各レベルの情報が順次読み込まれることで、複雑なレポートの自動生成が実現されます。自動生成されるレポートはHTML形式で出力され、複数レベルのドリルダウン機能を備えたボックスチャート、歩留まりグラフ、損失パレート図、ウェーハマップ、確率分布、ヒストグラムなど、豊富なグラフィック表現により現場の状況を瞬時に把握できます。これにより従来の手作業でのデータ収集・集計作業が大幅に省力化され、エンジニアは高度な分析に注力することが可能となります。
下記の表は仕様ファイルの主要項目とその役割を整理しており、各項目が自動化システム全体の統合とリアルタイム視覚化にどのように貢献しているかを示しています。
項目 | 内容 | 役割 |
---|---|---|
パラメータ名 | 各測定項目の名称 | 分析対象の特定に不可欠 |
説明 | 個々のパラメータの詳細説明 | データの意味理解を促進 |
上限/下限スペック | 各項目の許容範囲 | 合否判定の基準となる |
目標値 | 理想的な生産条件 | 品質管理と改善の指標を提供 |
カテゴリ | 要約レポート向け分類情報 | データ整理とレポート作成の効率化に寄与 |
ポイント:上記表は、仕様ファイルに含まれる各項目が自動化システムの基礎データとしてどのように連携され、リアルタイムの視覚化や解析に寄与しているかを示しています。画像で示されたボックスチャートやその他のグラフィックは、本システムの機能を視覚的に把握するための重要な要素です。
手動で行っていたデータ集計作業を自動化し、業務の効率化を実現するための最適なソリューションです。膨大な仕様書やレポートデータの情報を効率的に整理し、必要な情報を素早く視覚化・取得できる「生成AI-OCRサービス」は、貴社の作業負担を大幅に軽減します。
今すぐこのサービスの導入を検討し、現場でのデータ管理を革新しましょう。
使用技術とシステム連携
本自動化システムは、SASマクロ言語、SAS/GRAPH、SAS/QCなどの高度な統計解析ツールを駆使しており、Perlプログラムや構成ファイルを活用してSAS実行環境との連携を行っています。システムはCGIインターフェースにより、ユーザーがカスタマイズ可能なオンザフライレポートを生成でき、既存のERPやMESシステムとの柔軟なデータ連携も実現されています。以下の箇条書きは、本システムで採用される主要技術と、それぞれの役割、連携方法を具体的に示しています。
- SASマクロ言語:レポート自動生成ロジックの中核を担い、複雑な計算やグラフィック生成を実行
- SAS/GRAPH:各種グラフィック(ボックスチャート、ウェーハマップ等)の生成を担当
- SAS/QC:品質管理および統計的工程制御の指標算出に活用
- Perlプログラム:SAS実行の自動化およびデータ前処理を担う
- CGIインターフェース:ユーザーによるオンザフライレポートのカスタマイズ生成を容易にする
また、システムはAPI連携やデータ変換機能を備え、ERPやMESとの統合運用を実現しています。
RoviSysによる半導体業界のリアルタイム化
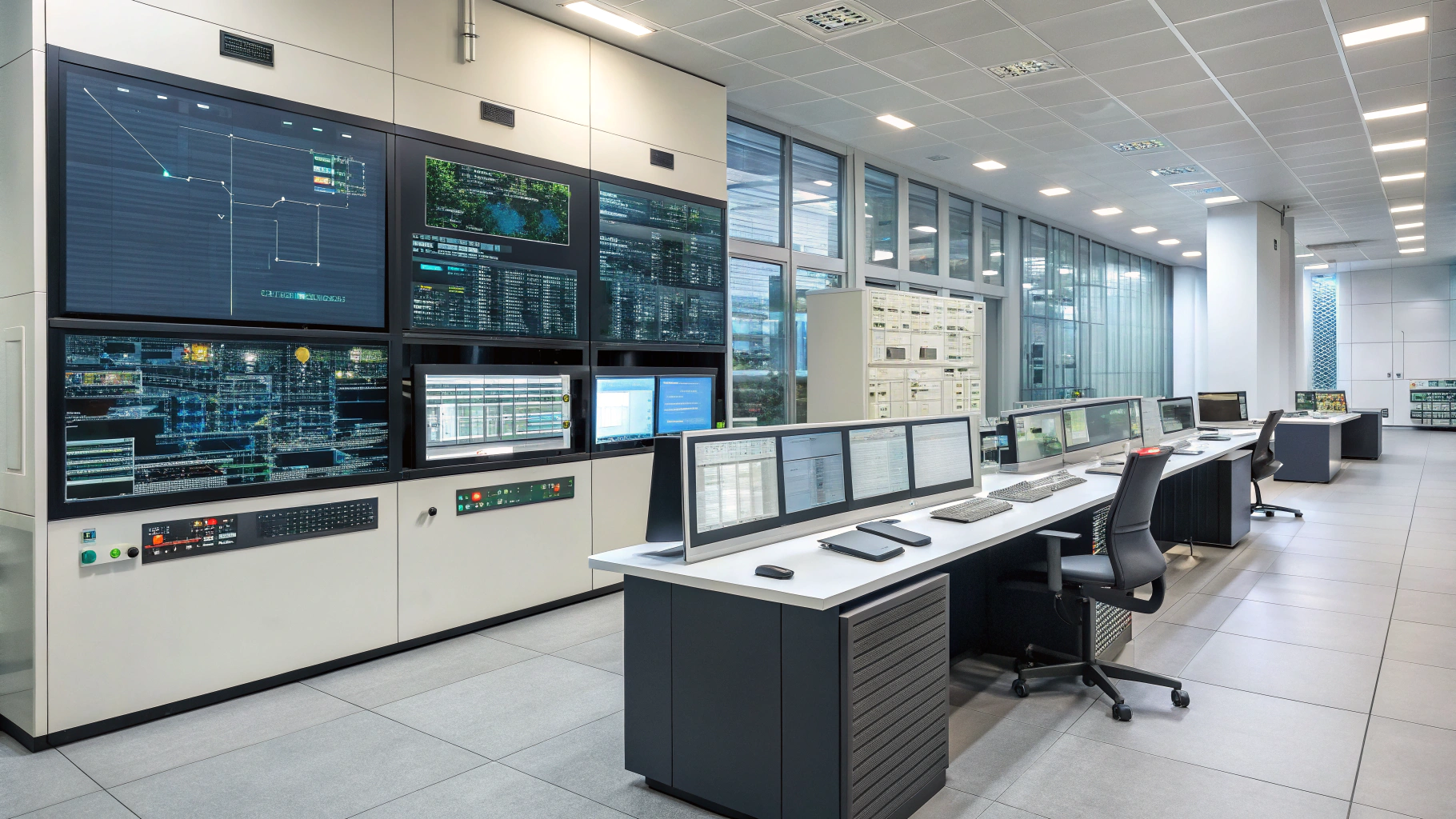
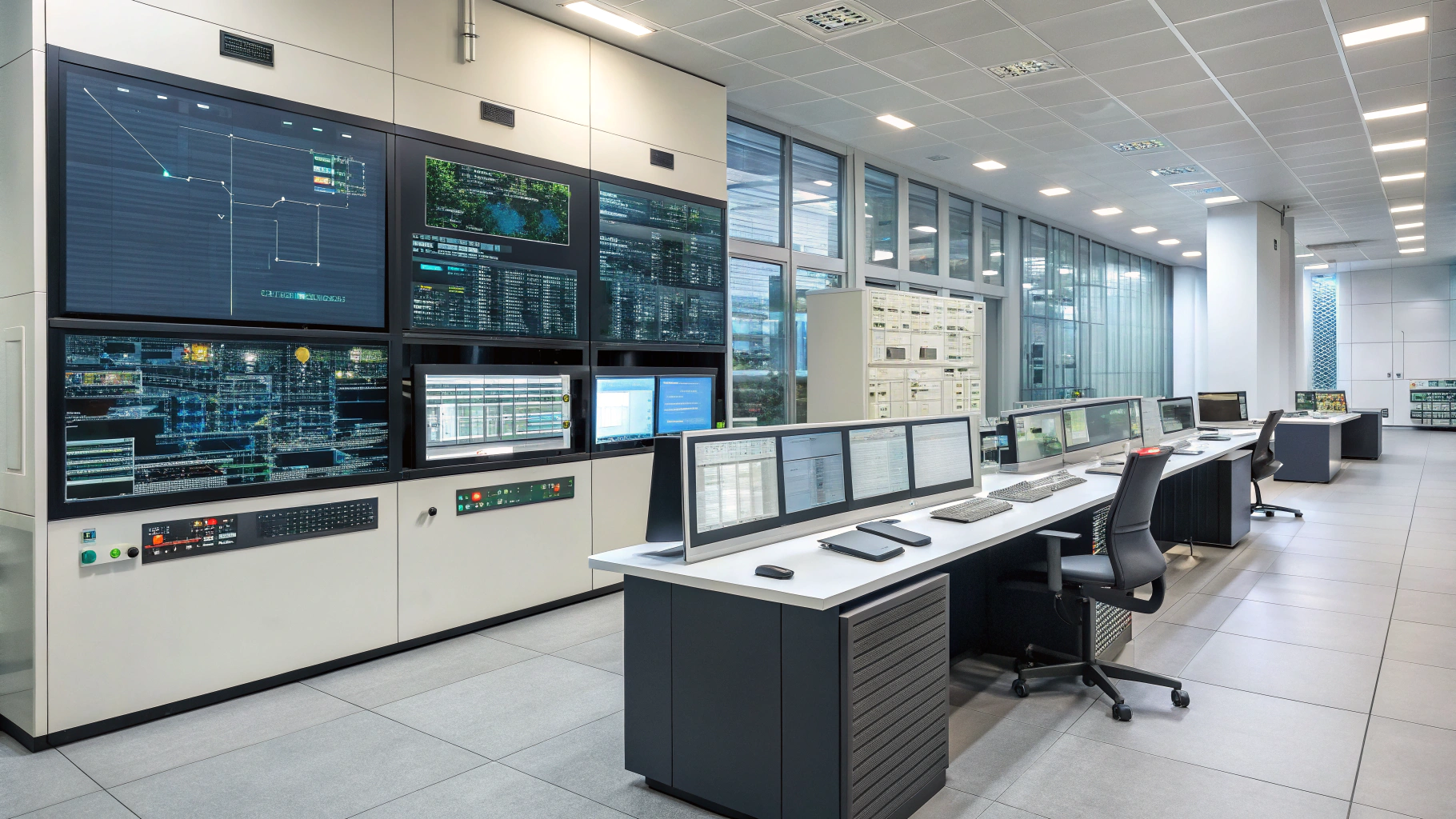
リアルタイムインテリジェンスの導入事例
半導体市場の需要急増に伴い、装置メーカーは従来の手動入力やExcel管理によるデータ管理の限界を克服する必要がありました。リライト元記事に記載されている米国拠点の化学機械製品および装置メーカーは、手動入力によるエラーや反映遅延が製造工程全体に悪影響を及ぼしていたため、RoviSys社のソリューションを採用しました。このシステムは、FactoryTalk Transaction ManagerやFTHistorian SQLデータベースと連携し、各原材料およびバッチの詳細な材料情報を自動でキャプチャするとともに、ERPシステムへ即時に反映する仕組みを実現。これにより、従来の手動入力によるエラーが大幅に削減され、材料割合の自動計算と消費データのリアルタイム更新が可能になりました。結果として、製造現場では生産ラインのスループット向上、歩留まりの改善、出荷スピードの加速が確認され、グローバルな需要に柔軟かつ迅速に対応する体制が構築されています。
プロセス | 従来方式 | RoviSys導入後 |
---|---|---|
データ収集 | 手動入力、Excel管理 | 自動化されたリアルタイム収集システム |
エラー発生率 | 高い傾向 | 大幅な低減(例:10%→2%) |
反映速度 | 遅延あり | 即時反映 |
システム連携 | 部分的統合 | シームレスな統合 |
課題とその解決策
急激な需要増加とそれに伴う材料管理の複雑化により、従来の手動入力方式ではヒューマンエラーが頻発し、生産性低下や品質不良のリスクが生じていました。リライト元記事に示されているように、Dell Boomiシステムを介した生産データの標準化は実施されていたものの、材料管理は完全な自動化とは程遠い状況でした。そこでRoviSysは、複数のデータソースを統合し、原材料情報の自動キャプチャおよびERPとのリアルタイム連携を実現するシステムを構築。以下の箇条書きは、解決策の具体的要点です。
- 自動データキャプチャ:各原材料の仕様情報を瞬時に読み取り、データベースへ自動反映
- リアルタイム連携:ERPシステムと即時データ連携し、現場状況を即反映
- エラー排除:手動入力を徹底排除し、ヒューマンエラーを大幅に削減
- 統合管理:複数のデータソースを一元管理し、全体の透明性を向上
また、下記画像は、実際の製造現場において自動化された材料管理システムがどのように稼働しているかを示すもので、従来の手作業に比べて大幅な効率化とエラー削減を実現している点が視覚的に確認できます。
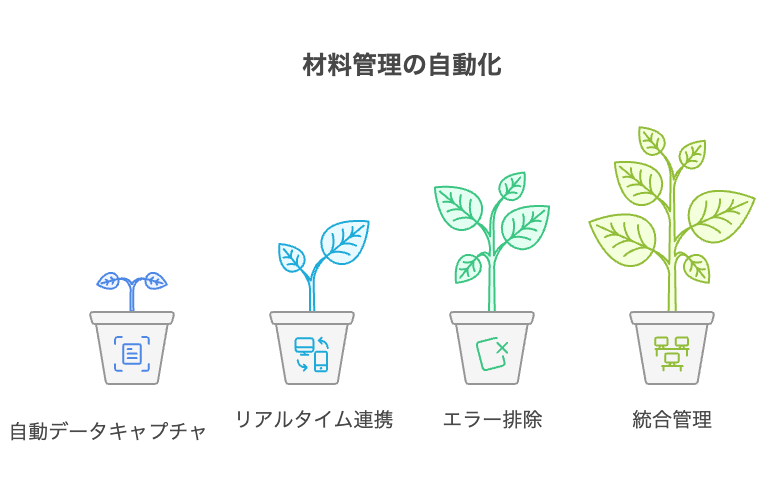
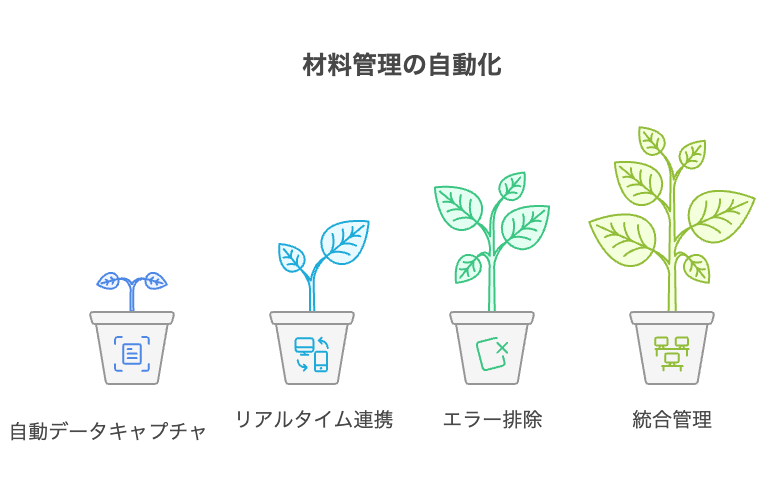
RoviSysの専門知識とソリューション
RoviSysは、長年にわたるバッチおよびプロセス製造の経験と専門知識を背景に、S88バッチ制御を活用したプロセスのモジュール化・自動化技術を提供しています。リライト元記事にもあるように、RoviSysは化学物質収支計算の複雑な側面を網羅し、現場に常駐することなく遠隔操作でのデータ管理と追跡を可能にしました。たとえば、FactoryTalk Transaction ManagerおよびFTHistorian SQLデータベースと連携したシステムにより、Pick List Webアプリケーションから各原材料やバッチ情報を直感的に整理し利用できる環境を整えています。
- プロセスのモジュール化:工程ごとに独立した管理を実現し、容易な変更・拡張が可能
- データ統合:複数のシステム間でデータをシームレスに連結し、全体の運用の透明性を向上
- ユーザーフレンドリー:Webベースの直感的なインターフェースにより、必要な情報へ迅速にアクセス可能
下記画像は、RoviSysによる遠隔データ管理システムの運用例を示しており、現場と同等の情報をリアルタイムに取得できる仕組みが、グローバル市場における迅速な対応を支えていることを強調しています。
Opcenterによる半導体製造プロセスの最適化
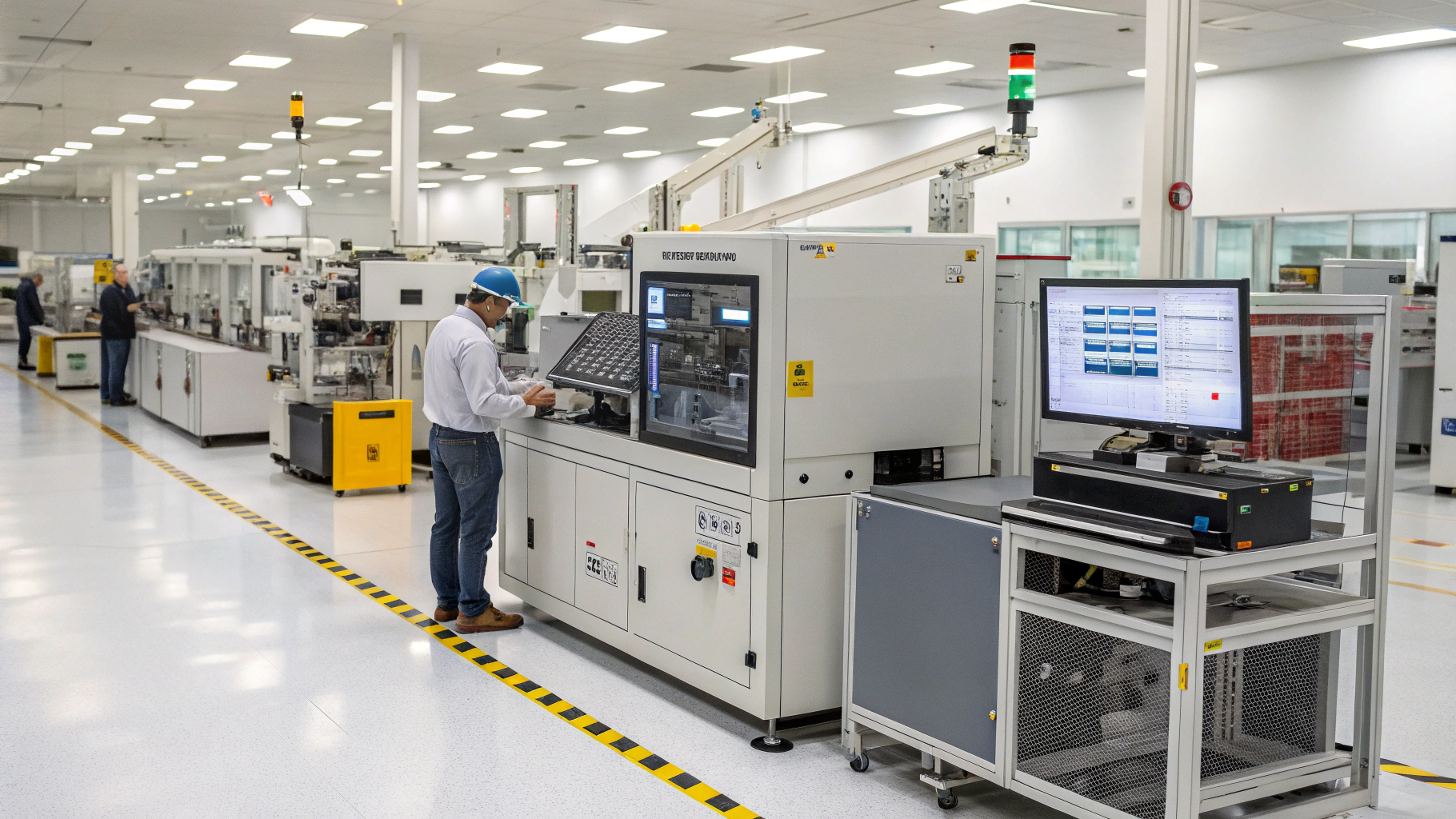
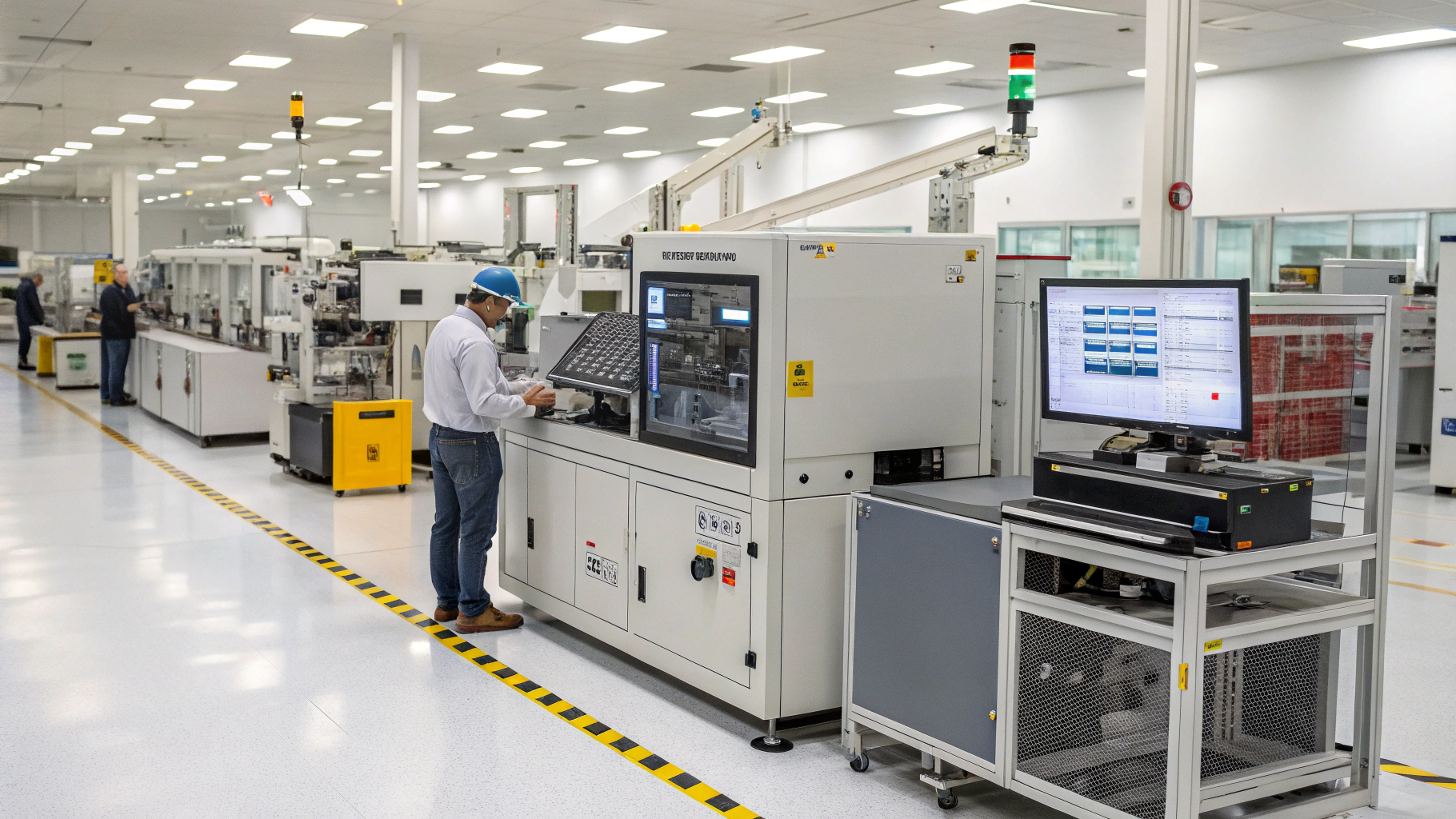
Opcenter Execution Semiconductorの機能
Opcenter Execution Semiconductorは、半導体製造工程におけるスループット、歩留まり、コストの最適化を実現するMES(製造実行システム)です。システムは、装置センサーから直接データを収集し、各ウェーハや投入材料のトレーサビリティを確保するだけでなく、現場オペレーターが迅速に意思決定できるよう、再利用可能なワークフローも構築しています。下記の表は、Opcenter Execution Semiconductorの主要機能とその効果を分かりやすく示しており、各機能が現場の運用効率と信頼性向上にどのように寄与するかを明確化しています。
機能 | 説明 | 効果 |
---|---|---|
現場統合 | 製造装置、センサー、ERPとの連携を実現 | 運用可視性と効率の大幅向上 |
再利用可能なワークフロー | レシピ、マスク、ツールのモデル化と一元管理 | 変更管理を簡素化し、迅速な工程展開を支援 |
デジタルツイン | 実生産データと連動したリアルタイム解析 | 歩留まり向上と設備効率の最適化に寄与 |
下記画像は、Opcenter Execution Semiconductorが現場でどのようにセンサーや各装置からのデータを統合しているかを視覚的に示しており、デジタルツインとして再現される全体のデータフローが現場オペレーターにリアルタイムの意思決定支援を提供する様子が分かります。
デバイスレベルの追跡とトレーサビリティ
半導体製造工程では、各工程で生成されるデータ量が飛躍的に増加する中、デバイスレベルの詳細な記録と家系図の追跡が不可欠です。Opcenter Execution Semiconductorは、装置センサーから取得した各ダイ、リードフレーム、エポキシ、ボンドワイヤ等の原材料データをリアルタイムで一元管理し、追跡精度を向上させています。これにより、万一のトラブル発生時に速やかに原因を特定し、迅速な対策が可能となります。
- 詳細な記録:各工程で生成されるデータを細部まで記録し、全デバイスの製造履歴を管理
- リアルタイム更新:装置センサーからのデータが即時反映され、常に最新情報を提供
- 家系図管理:各デバイスの起源から出荷までの履歴を一元的に管理し、完全なトレーサビリティを実現
また、下記画像は、デバイスレベルでの詳細な追跡がどのように行われているかを示すもので、各デバイスの履歴がデジタルツインとして再現される仕組みが視覚的に理解できるようになっています。
再利用可能なワークフローの活用と現場管理
Opcenter Execution Semiconductorは、レシピ、マスク、ツールなど複雑なプロセスフローや仕様をモデル化し、再利用可能な形で保存することで現場作業の効率向上を実現しています。システムは、各工程の指示書や工程情報を一元的に管理し、変更が発生した際には全ラインへ自動で即時反映される機能を備えています。これにより、手動更新によるエラーが排除され、統一された運用管理が実現されます。また、装置メンテナンス、NPI、変更管理システムとの統合により、オペレーターは常に最新かつ正確な制御情報を得ることができ、設計通りの製造を確実に行う環境が整備されています。
- 一元管理:各工程の指示書や情報が統合され、変更管理が容易に実施される
- 自動更新:プロセス変更が全ラインに自動反映され、エラーが防止される
- 現場統合:各装置やシステムとの連動により、リアルタイムで製造状況を正確に把握
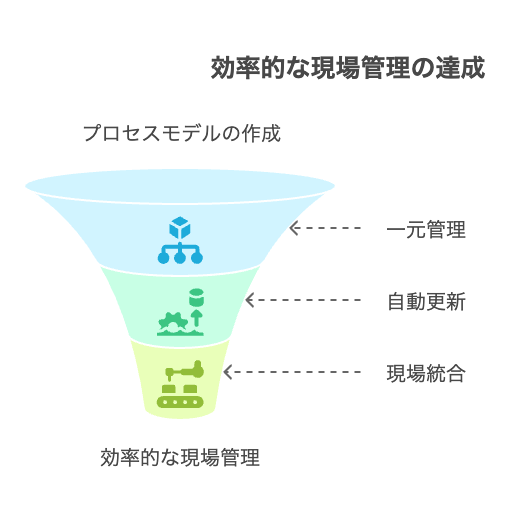
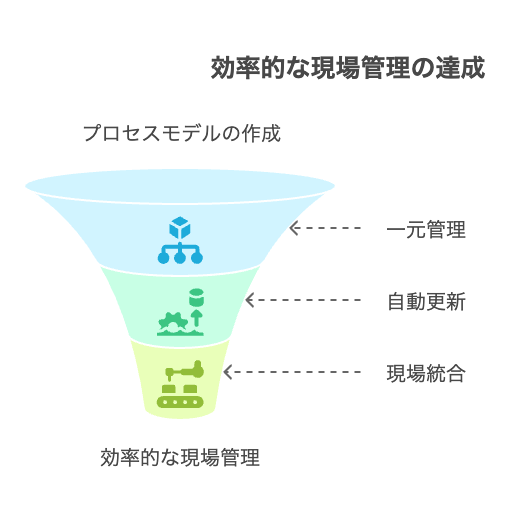
IBM SiView Standardによる半導体製造の高度化
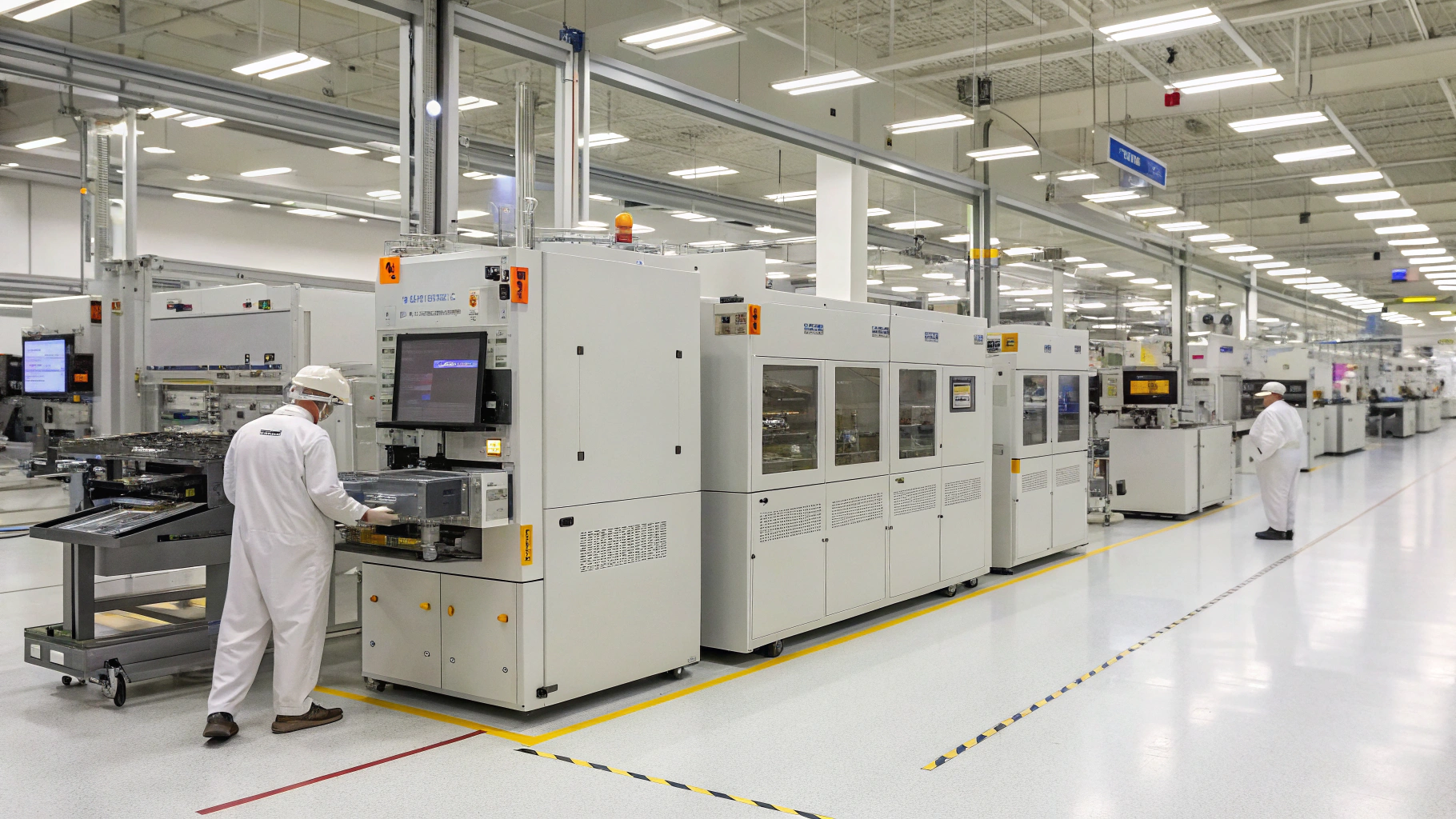
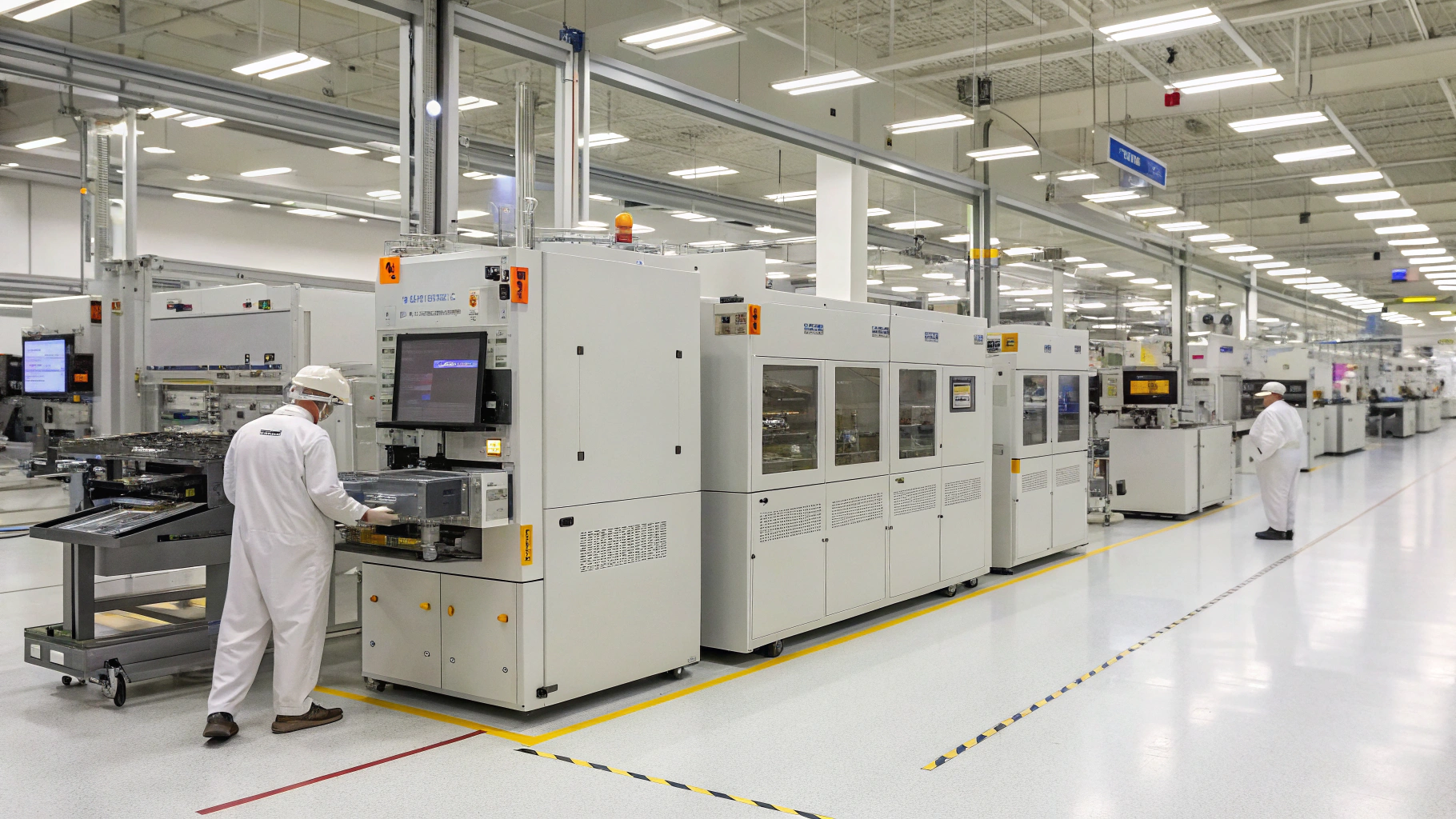
IBM SiView Standardの概要と詳細な機能
IBM SiView Standardは、グローバルに展開する半導体製造現場をよりインテリジェントかつ高度に最適化するためのソリューションです。シングルウェーハ制御およびキャリア内複数ロット処理の完全自動化を実現し、運用効率の向上を支援します。システムは、マテリアルマネージャー、センスアンドレスポンス、高度なプロセス制御、高可用性スケーラビリティ、マシン監視プログラムなど、幅広い機能を統合しています。これらの機能は、各工程における自動化とリアルタイム監視を可能にし、全体の製造ラインの最適化に大きく寄与します。
下記の表は、SiView Standardの主要な機能と具体的事例を整理して示しており、実績としては1,300日以上の連続稼働実績など、定量的な成果が確認されています。
機能 | 説明 | 具体的事例 |
---|---|---|
マテリアルマネージャー | ウェーハ、ロット、装置などのオブジェクトを統合管理 | リアルタイム生産制御とトレーサビリティの向上 |
センスアンドレスポンス | 工場内のイベントを検出し自動対応するワークフローエンジン | 需要変動に応じた自動ルール実行 |
高度なプロセス制御 | 外部数式モデル(例:MATLAB)のライブラリ統合 | 複雑な制御モデルの迅速処理 |
高可用性スケーラビリティ | クラスタリング機能によるノンストップ運用 | 1,300日以上の連続稼働実績 |
また、SiView Standardは、半導体テストデータ管理分野においてもRITdbワーキンググループの提案を取り入れ、柔軟なデータ管理とリアルタイム解析を実現しています。システムは、戦略的ソーシングやエンタープライズリソースプランニングと統合され、グローバルな製造ライン全体の運用効率を大幅に向上させています。
SiView Standardのメリットと実績
IBM SiView Standardは、約200の即時利用可能なファブ運用シナリオをサポートし、主要なSEMI標準やMCSベンダーとの統合実績により、業界標準としての信頼性を確立しています。 システムは、単一ウェーハ制御と複数ロット処理の自動化を通じて、大幅な運用効率の向上と高い信頼性を実現しており、Red Hat Enterprise Linuxを活用したハイブリッドクラウド環境下でも運用が可能です。以下の箇条書きに、SiView Standardがもたらす主要なメリットをまとめています。
- 完全自動化:単一ウェーハ制御と複数ロット処理の自動化により大幅な運用効率向上
- 業界標準準拠:SEMI標準および主要MCSベンダーとのシームレスな統合
- 高可用性:1,300日以上の連続稼働実績に裏打ちされたシステムの安定稼働
- グローバル統合:複数拠点にまたがる統合管理で市場変化に柔軟に対応
BM SiView Standardを活用して、運用効率向上やシステムの自動化が進む一方、業務の時間短縮やコスト削減が可能です。大量のデータを取り扱う際、生成AI-OCRサービスを活用すれば、PDFカタログやその他のドキュメントから商品情報を迅速かつ正確に抽出できます。これにより、手作業でのデータ入力作業を大幅に削減できます。特に100ページ以上のPDFの自動処理が可能で、業務の効率化に大きく貢献します。これ、もう任せたいかも…
半導体テストデータ:RITdbとSTDF
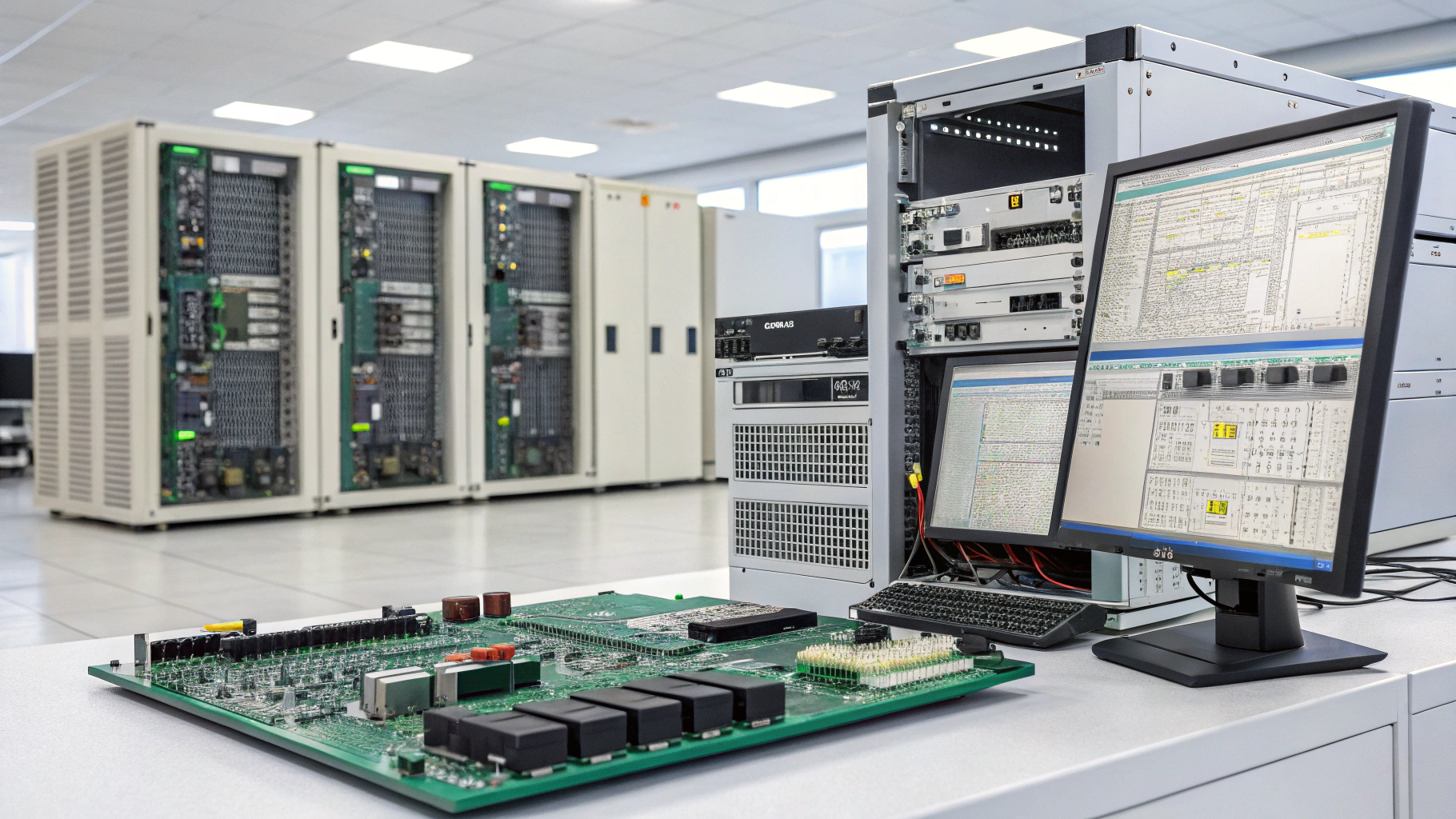
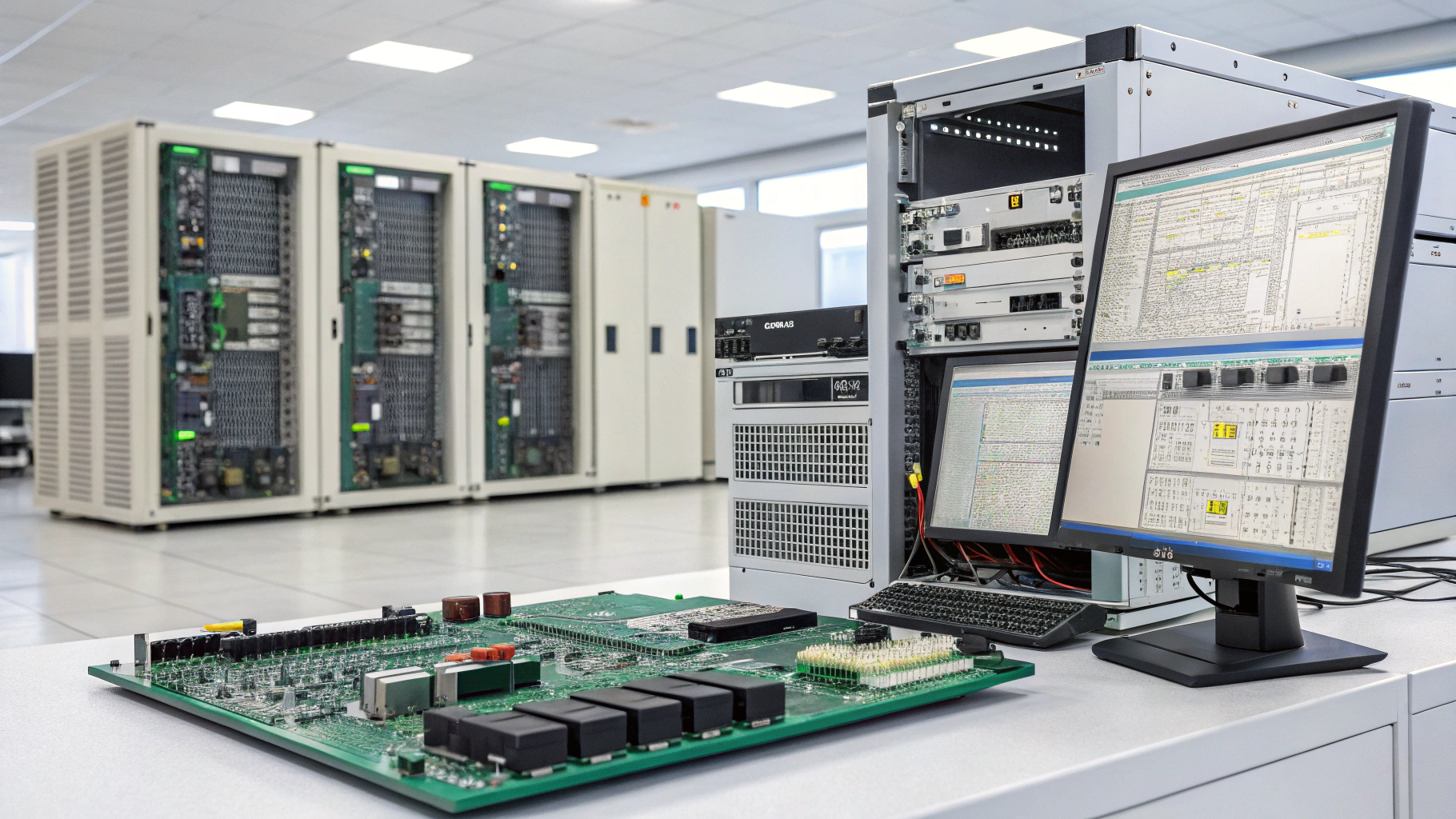
リッチインタラクティブテストデータベース(RITdb)の紹介
リッチインタラクティブテストデータベース(RITdb)は、半導体製造およびテストサイクルの全工程において、チップに付随するメタデータの一元管理を目的とした標準的なデータベースとして提案されています。リライト元記事に記載されている通り、RITdbはSQLiteを基盤とし、各エントリをシーケンス、entityID、indexID、名前、値、value2の6列で管理することで、柔軟かつ標準化された形式でデータを保存できます。これにより各テストプロセスで生成されるメタデータが統一的に管理され、リアルタイム解析や適応テストに活用されます。また、MQTTプロトコルに基づくストリーミング通信を採用することで、テストセル間で双方向のリアルタイムデータ送受信が可能となり、システム全体の効率を飛躍的に向上させています。
項目 | 内容 | 利点 |
---|---|---|
データ構造 | シーケンス、entityID、indexID、名前、値、value2 | 柔軟かつ標準化された管理が可能 |
技術基盤 | SQLite | 軽量で高速なデータベース運用 |
通信プロトコル | MQTTベースのストリーミング | 双方向でリアルタイムなデータ送受信を実現 |
WAT/PCMデータの概要と視覚化
ウェーハ受け入れテスト(WAT)またはプロセス制御監視(PCM)データは、製造最終段階でファブにより生成される、極めて重要なデータ群です。リライト元記事に記されている通り、これらのデータは通常40~100のテスト結果が各ウェーハサイトで記録され、主要なパラメータの一貫性を監視する目的で活用されます。WATデータは、CSVやExcel形式により小容量で提供され、迅速なデータ解析と視覚化に適しています。特に歩留まり管理システム(YMS)との連携では、異常値の早期検出や工程改善に大きく貢献します。
- トレンド分析:各ウェーハの同一サイトのパラメータを同色のトレンドラインで表示し、異常箇所を直感的に把握
- ボックスプロット:複数ロットのデータ分布を箱ひげ図で示し、特定ロットの異常を検出
- 相関チャート:WATパラメータ平均とウェーハソート故障率の相関関係を示し、高リスクロットを特定
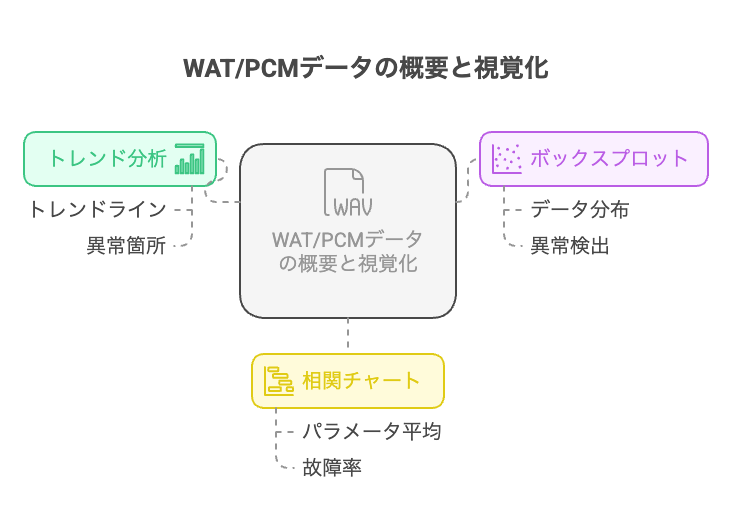
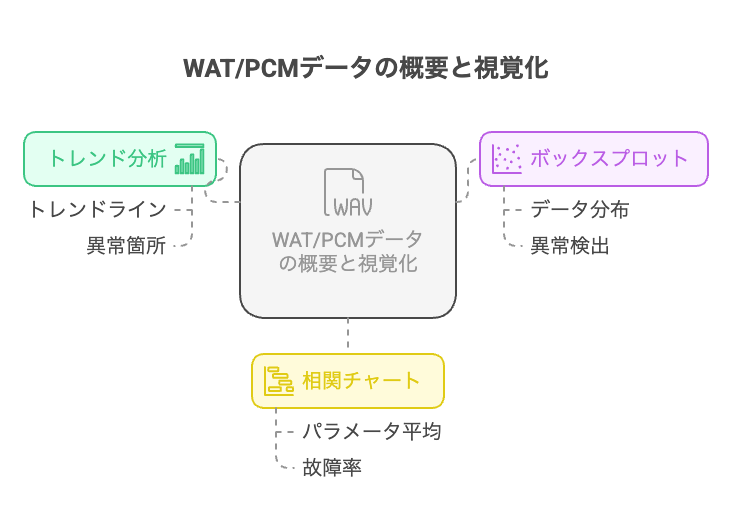
まとめと今後の展望
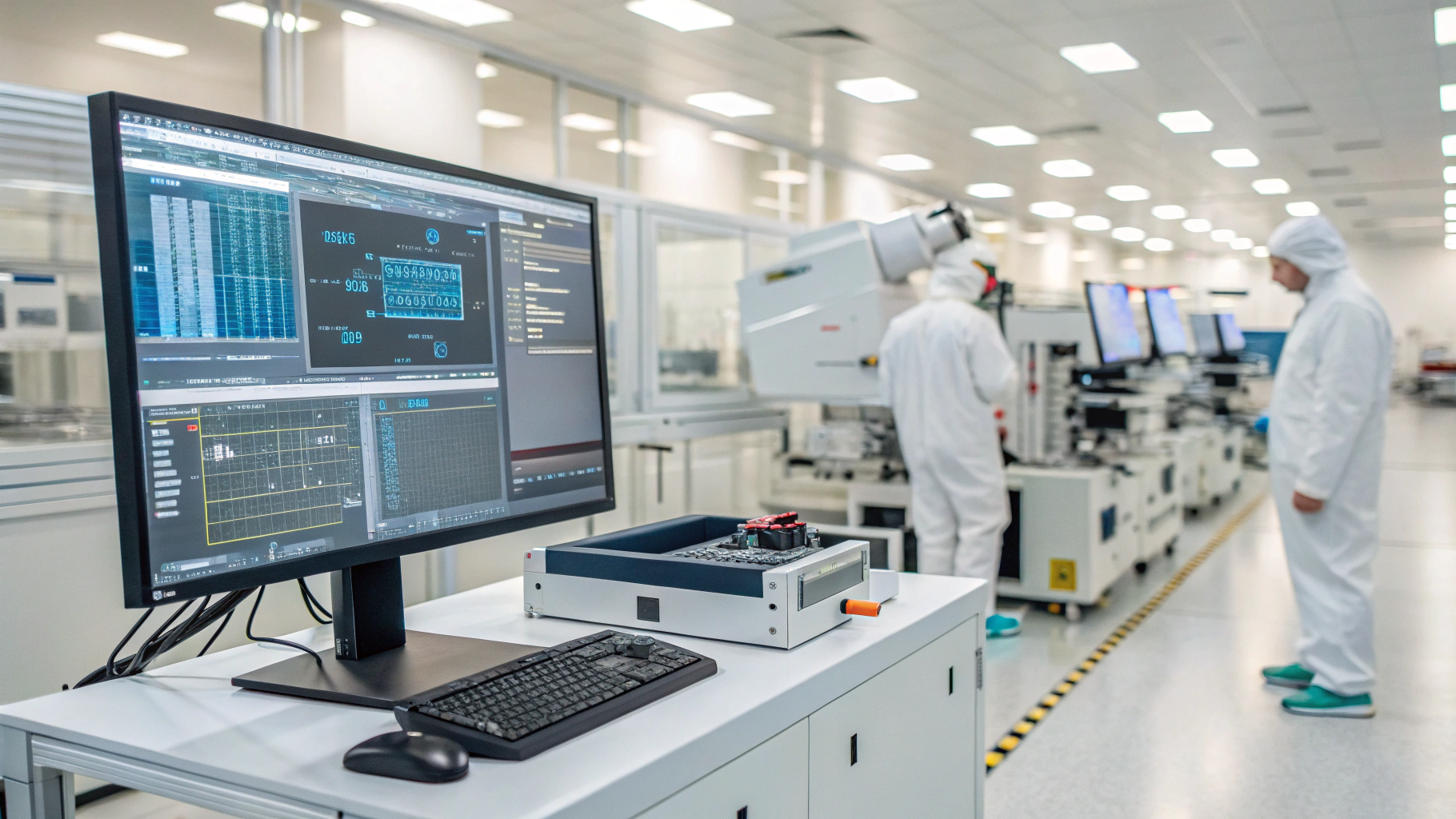
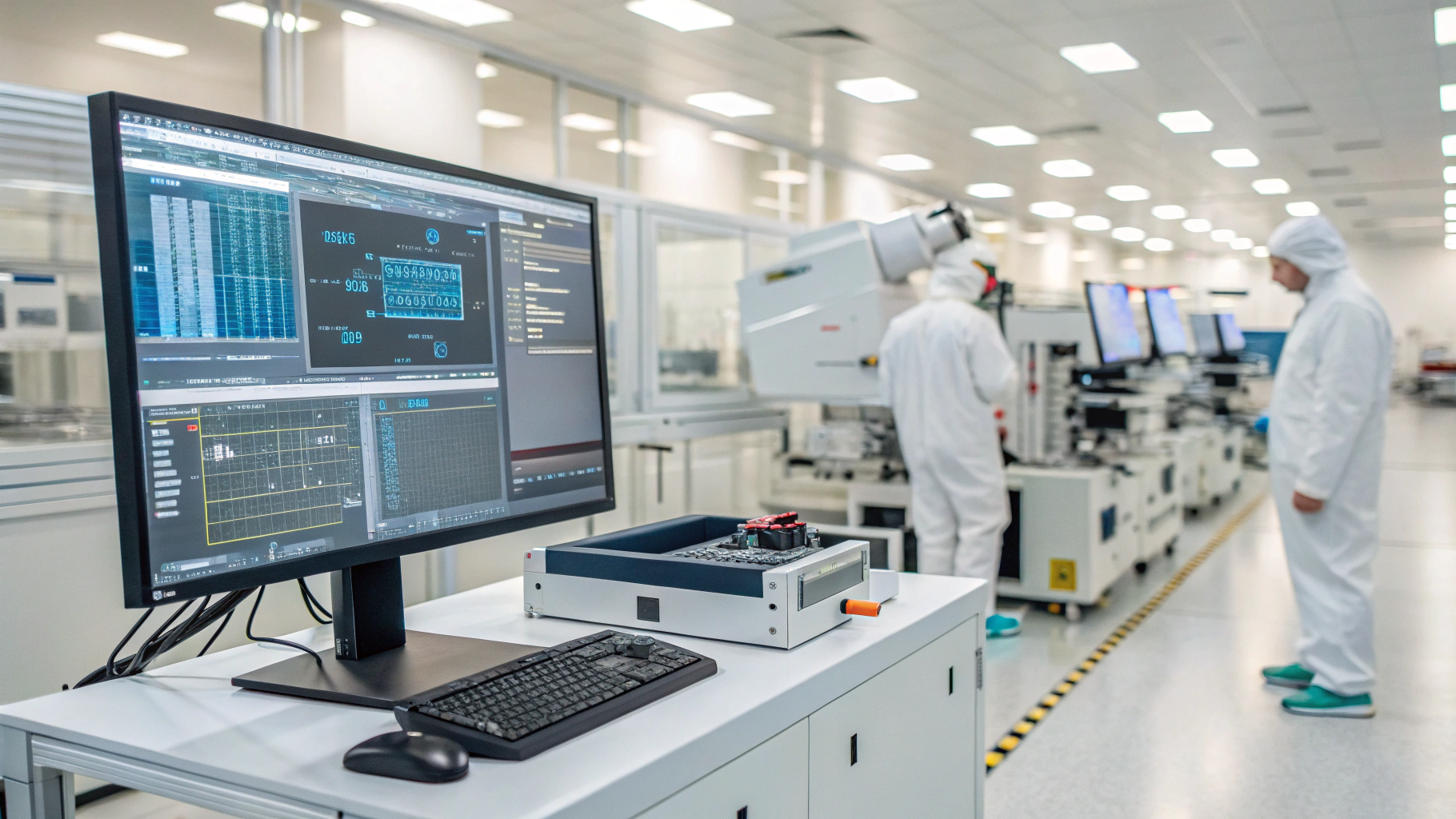
本記事では、半導体仕様書データベース化自動化システムを中心に、RoviSysによるリアルタイムインテリジェンス、Opcenterによる製造プロセスの最適化、IBM SiView Standardによる高度な製造管理、そしてRITdbおよびWAT/PCMデータの各システムについて解説しました。それぞれのシステムが、従来の手作業による入力やデータ管理の課題を解決し、定量的な成果―例えばエラー発生率の低減や連続稼働日数の向上―を実現していることが確認できます。各システムはいずれも、最新技術を活用した自動化とリアルタイム解析により、製造現場の効率化、品質管理、そして市場変化への柔軟な対応を可能にしています。
今後、これらの技術はさらに深化し、生成AIエンジニアを含む専門家にとっても、具体的な設定例や処理フローの可視化を通じた技術的理解の向上、さらなる効率改善に寄与することが期待されます。各システムの統合と運用実績は、半導体製造のデジタルトランスフォーメーションを推進する重要な要素として、今後の展望においても注目されるでしょう。